Table of contents:
Comparing Hydraulic Versus Electric Servo Drives
Regenerative Braking and Power-factor Correction Savings
Load-adaptive Rotor Speed Algorithms for Heterogeneous Feedstocks
Case Study: 12% Energy Savings in a Paper Mill Retrofit
Comparing Hydraulic Versus Electric Servo Drives
Selecting the drive system for a single shaft shredder is a critical decision that can drastically impact efficiency. Hydraulic drive systems, once a standard for heavy-duty applications, offer high torque but often fall short with energy efficiency as they tend to consume more power during operation. On the contrary, electric servo drives provide precise control over the motor's speed and torque while reducing overall energy consumption. Electric servo drives also have the added benefit of lower noise levels, making them an attractive option for environments focused on sustainability and workplace comfort. They’re increasingly favored by single shaft shredder manufacturers for applications requiring both consistency and energy efficiency, balancing cost and performance effectively. When paired correctly, they enhance shredding capabilities even for heterogeneous materials, maintaining uniform output size and reduced power usage.
Regenerative Braking and Power-factor Correction Savings
Advanced electric servo drives unlock the potential of regenerative braking in single shaft shredder machines. This technology recaptures energy usually wasted as excess heat during the shredding process and redirects it for later use. By leveraging regenerative braking, businesses can significantly cut energy costs, particularly in operations requiring frequent starts and stops. Furthermore, single shaft shredders with power-factor correction features optimize energy usage by regulating the draw on the power grid. This is paramount in reducing energy waste, lowering electricity bills, and decreasing the environmental impact. Together, these technologies reflect a move toward efficient, eco-conscious designs from single shaft shredder manufacturers and service providers.
Load-adaptive Rotor Speed Algorithms for Heterogeneous Feedstocks
One of the most advanced developments in single shaft shredders comes through load-adaptive rotor speed algorithms. These algorithms dynamically adjust the rotor's speed depending on the type and density of the material being shredded. For heterogeneous feedstocks, this functionality minimizes unnecessary energy consumption and maximizes throughput. For example, lighter materials like paper or foam require lower torque and speed, while denser materials such as wood or metals demand more power. The algorithm detects material changes in real time and automatically optimizes the rotor speed. This innovation not only ensures consistent shredding quality but also prevents motor overloads, prolonging the equipment's lifespan and reducing maintenance downtime.
Case Study: 12% Energy Savings in a Paper Mill Retrofit
A paper mill facing escalating operational costs decided to retrofit its old single shaft shredder with an electric servo drive equipped with regenerative braking and load-adaptive rotor speed algorithms. Before the upgrade, the system operated inefficiently, consuming excessive energy and requiring frequent repairs due to overheating issues. Post-retrofit, the results were remarkable. The paper mill reported a 12% reduction in kWh consumption within the first six months, translating to significant cost savings. The regenerative braking system recaptured over 15% of the energy produced during the rotor's deceleration phase, which was then redirected to power other parts of the machinery. Additionally, the load-adaptive rotor algorithms ensured precise energy use, customizing operations for various paper grades and reducing wear and tear on mechanical components. This transformation illustrates the tangible benefits of modern drive systems for single shaft shredders, making the case for investing in advanced features such as regenerative braking and adaptive algorithms.
Combining energy-efficient servo drives, regenerative braking, and load-adaptive technologies can revolutionize the performance of single shaft shredders, making them more environmentally friendly and cost-effective for industrial applications. Collaboration with established single shaft shredder manufacturers can ensure these innovations are accurately integrated into your operations. For industries aiming to maximize productivity while minimizing environmental impact, energy-efficient drive systems aren't just an upgrade; they're a necessity. By adopting these advanced technologies, businesses can stay ahead in an increasingly eco-conscious industrial landscape.
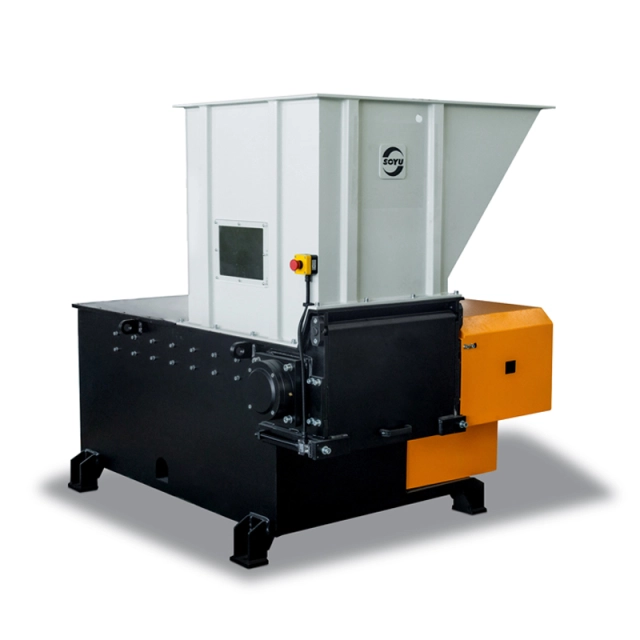
No comments:
Post a Comment