Table of contents:
Cutting and Shaping Titanium Plates: Methods and Best Practices
Welding Titanium Plates: Techniques and Considerations
Surface Treatment Options for Titanium Plates
Quality Control Measures in Titanium Plate Fabrication
Cutting and Shaping Titanium Plates: Methods and Best Practices
Cutting and shaping titanium plates involves specialized methods due to the material's unique properties, such as its strength and temperature sensitivity. One common technique is water jet cutting, which uses high-pressure water mixed with abrasive materials to slice through titanium without generating heat. Laser cutting is another option, ideal for intricate designs, and is frequently used by professional titanium sheet suppliers. Machining processes like milling and turning are also popular, though they require tooling optimized for titanium to reduce wear and tear. Precision and care are vital since any improper method can lead to burrs, inconsistent edges, or weakened material integrity, which can compromise the overall quality of the product.
Welding Titanium Plates: Techniques and Considerations
Welding titanium plates is a complex process that demands careful handling to maintain strength and prevent contamination. TIG (Tungsten Inert Gas) welding is the most commonly used technique due to its ability to create clean, high-quality welds. A crucial consideration during titanium welding is shielding the metal from oxygen and nitrogen exposure, as these can cause defects such as brittleness or porosity in the weld. This is often achieved using an inert gas like argon. Pre-weld cleaning is also essential to remove contaminants that might compromise the structural integrity. Reliable titanium plate supplier often conduct rigorous testing on welded products to ensure they meet industry standards.
Surface Treatment Options for Titanium Plates
Surface treatments enhance the performance and aesthetic appeal of titanium plates, making them suitable for diverse applications. Anodizing is one of the most popular surface treatments, offering improved corrosion resistance and the ability to add colors for identification or branding purposes. Polishing is another common method, used extensively in the medical industry for a smooth finish that minimizes bacteria adhesion. Surface roughening, such as bead blasting, is used to increase friction in applications like aerospace manufacturing. Many titanium plate suppliers offer customized surface treatments tailored to specific industry needs, allowing clients to achieve their desired balance of form and function.
Quality Control Measures in Titanium Plate Fabrication
Maintaining quality is paramount when fabricating titanium plates, particularly in industries such as aerospace and medical fields, where safety and precision are non-negotiable. Various quality control measures are employed to ensure the final product meets exact specifications. These include ultrasonic testing to detect internal flaws, X-ray inspection for welds, and chemical analysis to verify material composition. Reliable titanium sheet suppliers often provide detailed documentation and certifications, such as those adhering to ASTM B265 and ASME SB265 standards. By emphasizing stringent quality control, suppliers can ensure that their titanium plates perform exceptionally well in demanding environments.
In conclusion, sourcing titanium plates from reputable suppliers with a focus on quality control is essential for ensuring optimal performance across various industries. By relying on advanced testing methods and adhering to recognized industry standards, these suppliers provide materials that meet the highest levels of reliability and durability. This commitment to excellence not only enhances the integrity of the final product but also builds trust and confidence among clients, making titanium an indispensable choice for critical applications.
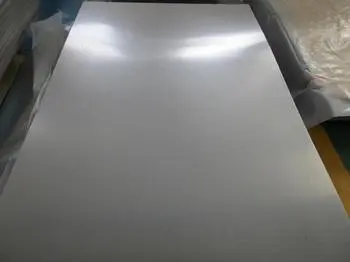
No comments:
Post a Comment