Table of contents:
The Role of Tungsten Carbide in Extending Tool Lifespan
How Tungsten Carbide Welding Rods Improve Cutting Efficiency
Case Studies: Industries Benefiting from Tungsten Carbide Welding Solutions
Tips for Integrating Tungsten Carbide Welding Rods into Your Manufacturing Process
The Role of Tungsten Carbide in Extending Tool Lifespan
Tungsten carbide is a composite material renowned for its strength and durability. With a hardness rating that surpasses most other metal alloys, it is uniquely suited to handle the abrasive and wear-intensive environments of industrial tools. The particles within tungsten carbide offer enhanced impact resistance, allowing tools to remain in service longer without succumbing to significant wear. Research has shown that tools reinforced with tungsten carbide welding rods can last up to three times longer than tools made from traditional materials. This translates to fewer replacements, less downtime, and significant cost savings for businesses in industries like mining, construction, and manufacturing. By opting for tungsten carbide, industries can extend the life of their equipment and tools, improving operational efficiency and reducing maintenance costs.
How Tungsten Carbide Welding Rods Improve Cutting Efficiency
An important advantage of using tungsten carbide welding rods is their extraordinary ability to improve cutting efficiency. The high density and strength of tungsten carbide make it ideal for crafting rods that maintain sharp cutting edges even under challenging conditions. These rods are particularly suitable for cutting and drilling applications requiring precision and consistency, such as machining or trenching. Tungsten carbide also maintains its structural integrity under high temperatures, which means tools stay sharper for longer and resist deformation. Furthermore, the material’s abrasive qualities allow for smooth cuts with minimal resistance, leading to faster processing times and improved results. For businesses, this means higher productivity and reduced reliance on multiple tool replacements during projects. By sourcing from trusted tungsten carbide rods suppliers, manufacturers can ensure optimal cutting efficiency while maintaining cost-effectiveness.
Case Studies: Industries Benefiting from Tungsten Carbide Welding Solutions
From heavy industries to niche manufacturing, tungsten carbide welding rods have revolutionized how businesses operate. For example, the mining sector frequently deals with tools for drilling through hard rock and other abrasive surfaces. By integrating tungsten carbide welding rods, miners have reduced tool wear by over 40%, saving significant downtime and repair costs. Similarly, the construction industry has seen improved operational performance in trenching and foundation drilling due to the rods' excellent wear resistance and cutting precision. Agricultural machinery, another key area of application, benefits from enhanced soil tilling tools capable of surviving prolonged outdoor use in tough environments. Additionally, metalworking businesses have achieved smoother machining operations with reduced heat damage, thanks to the rods' high thermal resistance. Across these examples, tungsten carbide welding rods have consistently demonstrated their ability to boost productivity and lower costs, establishing themselves as indispensable across various industries.
Tips for Integrating Tungsten Carbide Welding Rods into Your Manufacturing Process
For manufacturers eager to unlock the advantages of tungsten carbide welding rods, integration should follow a strategic approach. Start by partnering with reputable tungsten carbide rods suppliers who guarantee high-quality materials tailored to your specific needs. Before using the rods, evaluate your existing processes and identify the tools or applications requiring optimization. Consider factors like wear intensity, operating conditions, and the desired lifespan of tools to determine how and where tungsten carbide can be applied effectively. For welding, ensure you employ skilled technicians who are experienced in handling tungsten carbide materials, as precision and technique play a critical role in maximizing performance. Additionally, take advantage of the detailed specifications and guidelines often provided by suppliers, such as recommended particle sizes or coating options, to match your use case. Lastly, monitor the performance of your tools post-integration, as comprehensive data collection will guide future adjustments and ensure ongoing success.
In conclusion, the integration of tungsten carbide rods into your operations can significantly enhance the durability and efficiency of your tools when approached thoughtfully. By collaborating with reliable suppliers, understanding the specific needs of your processes, and leveraging expert craftsmanship, you can unlock the full potential of this high-performance material. Consistent monitoring and adaptation will ensure sustained improvements and long-term success, positioning your operations to meet even the most demanding challenges with confidence.
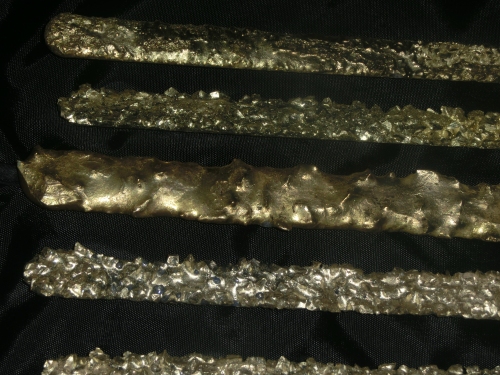
No comments:
Post a Comment